R&D
Technology Fusion of Glass and Chemistry. Developing new materials indispensable for high performance semiconductors based on Central Glass’s unique ideas
-
Article categories:
- A Fusion of Technologies
-
Related businesses:
- Electronic Materials
- Social issue
- Response to the increasing density of semiconductor devices
- Central Glass's engagement
- Development and mass production of chemicals that resolve production issues associated with circuit pattern shrinkage.
Semiconductors have become an indispensable feature of comfortable daily life. Semiconductor manufacturers face a number of issues as circuit patterns have become increasingly miniaturized as semiconductor device performance continues to advance. These trends have presented the opportunity for Central Glass to combine its long-cultivated technologies in glassmaking and chemical production to deal with the problem of circuit pattern collapse in the drying process after deionized water rinsing of wafer.an introduction
Background to Development
Starting around 2005, with the miniaturization of semiconductors, there was a growing awareness of a major problem: the collapse of high aspect ratio circuit patterns due to the surface tension of the cleaning fluid in the drying process which follows deionized water rinsing of wafer. The main approach to dealing with this issue at the time was to reduce the surface tension of the cleaning fluid, but this approach has its limits because it is impossible to bring surface tension down to zero.
One of Central Glass's technologies is in the area of imparting water repellence to the surface of automotive glass. We realized that we would be able to prevent pattern collapse by providing the surface of a semiconductor pattern with this same characteristic of water repellence. This development work resulted in a new product, Pattern KeeperTM.
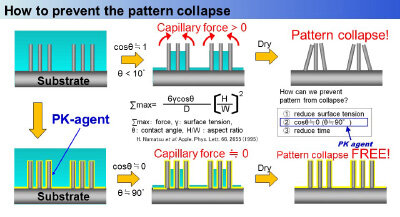
Challenges in Development
At the earliest stage of PK Agent development, it was necessary to reduce water repelling processing from temperatures of over 200°C for more than 15 minutes down to room temperature and less than 1 minute. It took a lot of trial and error work to overcome each obstacle, but in the end, we achieved the desired processing parameters. Our customers also demanded that we deal with trace metals and particles to meet what for us were unprecedented levels of quality control. Our development efforts extended from packaging to manufacturing methods to analytical methods.
Finding the Solution
By providing our customers with solutions to the problems they faced, we succeeded in developing a functioning product that the world had never seen before. In the mass production phase, as well, we were able to draw on our quality management experience in photoresist materials and semiconductor process gas production. Our research and plant personnel worked hard in a spirit of collaboration and with great determination to resolve each and every problem. In the end, we were able to go into the mass production of several different grades of the product.
Keys to Success
Technology Fusion of both Glass and Chemical Domains
In this development, a major factor in the success was the successful fusion of the technologies of the two departments: the Glass Research Center, which specializes in design development and functional evaluation, and the Chemical Research Center, which specializes in identifying the essence of manufacturing technology and analytical technology development. By taking advantage of their respective fields of expertise in glass and chemistry, the two R&D centers worked together to increase the speed of development while at the same time leading to major breakthroughs, which led to the birth of this unique and groundbreaking product.
Another important factor was that from the early stages of development, they were able to collaborate with the Intellectual Property Department to strategically secure intellectual property.
We will continue to carry out research and development that will lead to solutions for our customers by fusing the technologies of both the glass and chemical domains.